Without new workers rising through the ranks, craft would be in crisis. Companies making handcrafted home furnishings are leading the way in shaping the next generation.
When we started, no one aspired to this kind of work,” says Dave Dawson, the founder and president of Charleston, South Carolina–based custom lighting company The Urban Electric Co. A lawyer by trade, he started the business with his wife 15 years ago. “At the time, the big furniture companies were moving to the Philippines, textile mills were closing across North Carolina, and a whole generation of kids hadn’t taken shop class in school,” he says. “American manufacturing was on the ropes.”
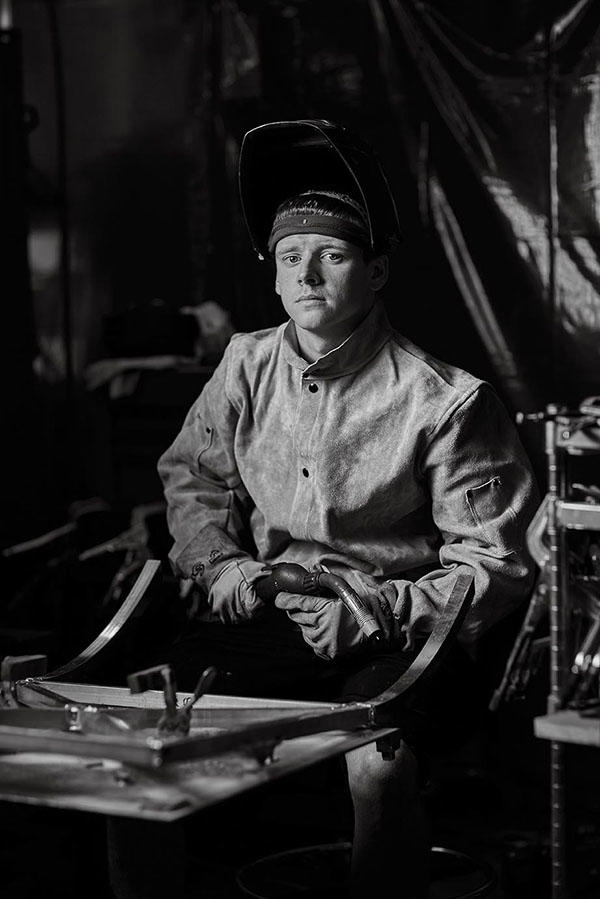
The search for employees to carry the torch for bespoke, bench-made product is happening across the country. New apprenticeship programs—more regimented than those of the past, with established curriculums and goals—have been a wellspring of new talent. “Without those skills passing on, craft dies,” says Dawson.
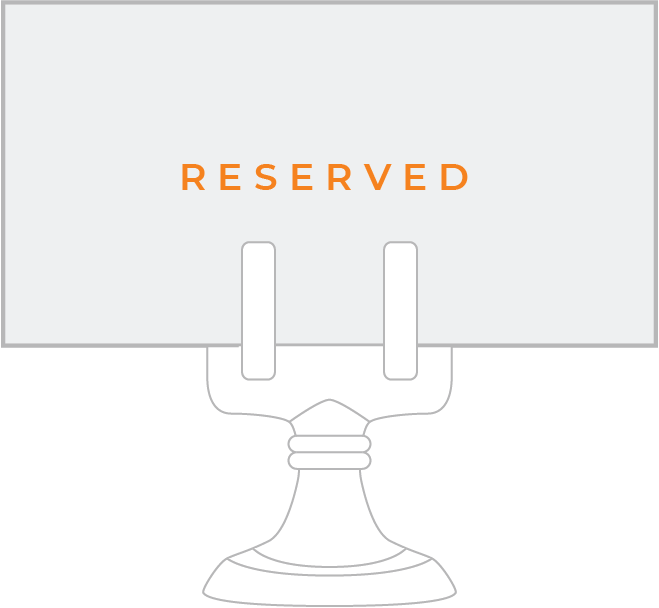
BOH subscribers and BOH Insiders.