Manufacturing is slowing being re-shored to the United States. As production costs rise abroad, the allure of “Made in America” grows.
Jonathan Bass shook hands with some 1,700 people at Badgley Mischka Home’s high-gloss booth at High Point Market this past October. And they all had the same thing on their minds, he says. “The first question they asked was, ‘Where is Badgley Mischka produced?’”
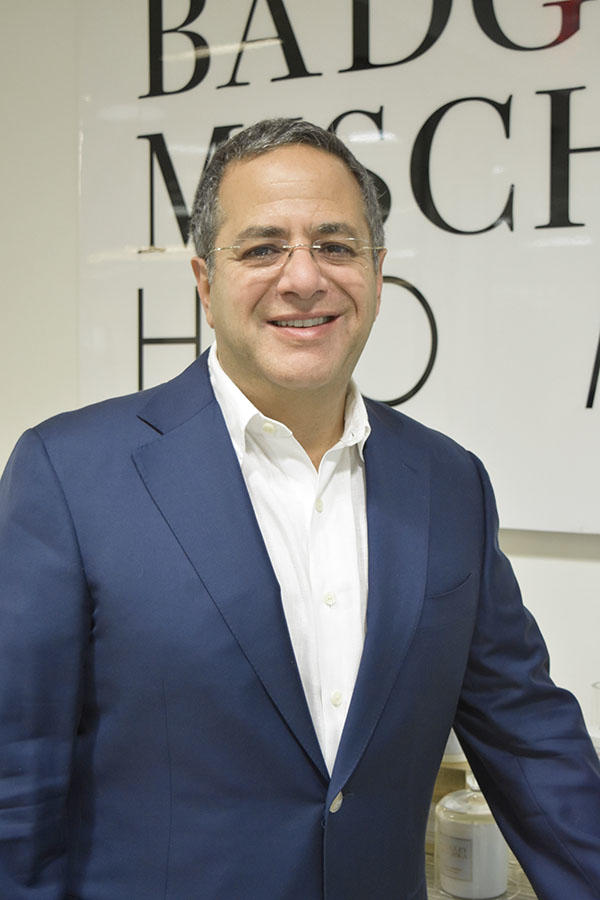
As owner of the manufacturing firm PTM Images, Bass is a huge proponent of domestic production. From 1995 to 2011, he produced wall decor, mirrors and frames in California’s San Fernando Valley; he launched hospitality and retail lines in 1998, which were produced in Asia until 2012. That was the year Bass “onshored everything,” he says, bringing the entirety of production to the U.S. and Mexico—including the Badgley Mischka Home collection, designed by fashion duo Mark Badgley and James Mischka and manufactured by PTM Images. He is currently developing a jacquard weaving factory in the U.S. to keep even more business stateside. “I’m very big on ‘Made in America,’” he says.
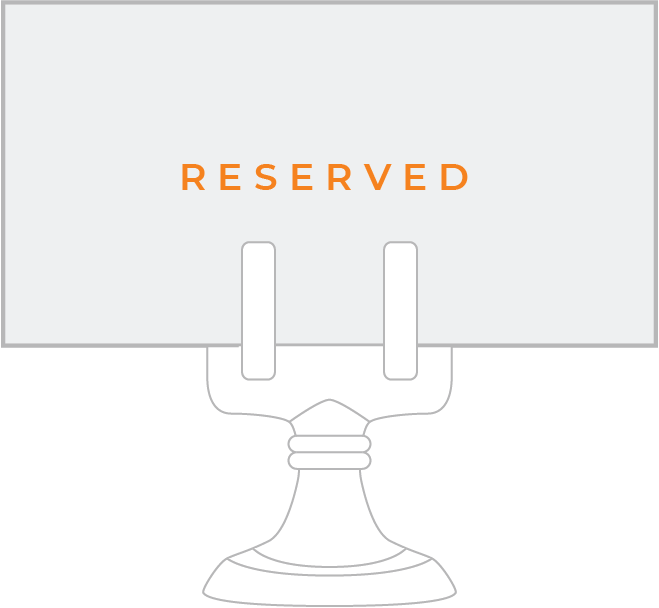
BOH subscribers and BOH Insiders.