If the phrase prefab home doesn’t conjure up images of health and serenity, there’s a reason for that. In Europe, manufactured housing can be a luxury product, but in the States, the concept has taken a long time to shake the stigma of association with low-cost homogeneity. However, the tides may be turning as a new generation of entrepreneurs explores the possibilities of prefab. This time around, the appeal isn’t just price point—it’s also wellness.
“You see more and more people with some sort of knowledge that there are more ways to build homes that won’t have a negative impact on your health,” says Brandon Weiss, chief innovation officer of three-year-old San Diego–based prefab building company Dvele, which raised a $14 million series A round last spring. The company has designed features to address air quality, mold, moisture, water filtration and nontoxic building materials; a Dvele-built home is also self-powered by solar panels (with a battery backup) and designed with efficiency in mind—a planet-friendly solution that fights climate change while increasing grid resilience. According to Weiss, its homes use 84 percent less energy than a conventional home.
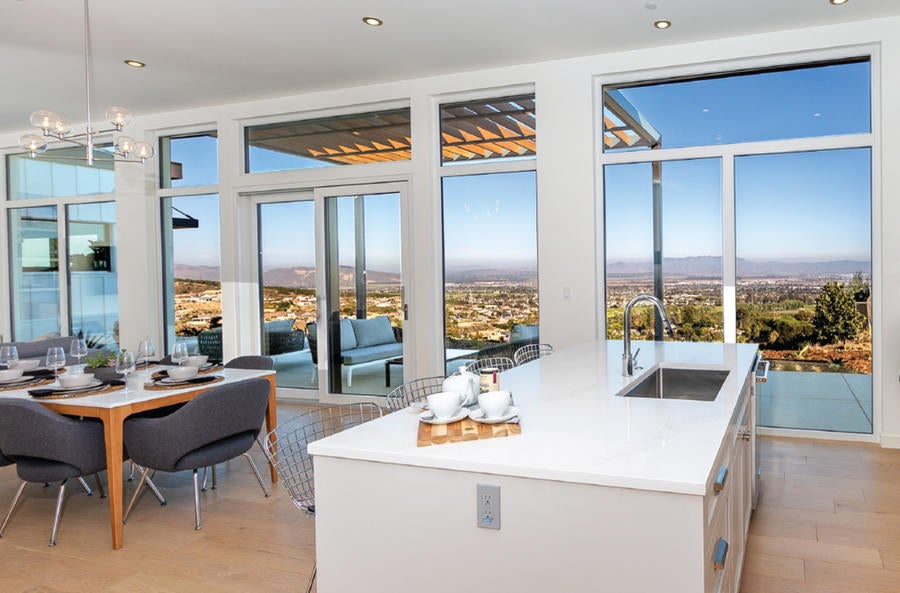
Another player in the market is Plant Prefab, a Rialto, California–based prefabricated design and manufacturing company that makes LEED Platinum factory-built homes that are sold on Amazon (which invested in the company last year). The company bakes efficiency into the home building process with its Plant Building System, pairing modular units with a compatible construction system that includes plumbing, electrical and finish materials—a combination that reduces costs, cuts down on manufacturing waste and results in shorter build times. “If you’re interested in building a new home, we make the process easier and more efficient,” says Steve Glenn, founder and CEO of Plant Prefab. “There’s a growing number of homes we’ve designed, or you can hire an architect and we can build their plan. You get the home faster and with lower costs than if you work with a local general contractor.”
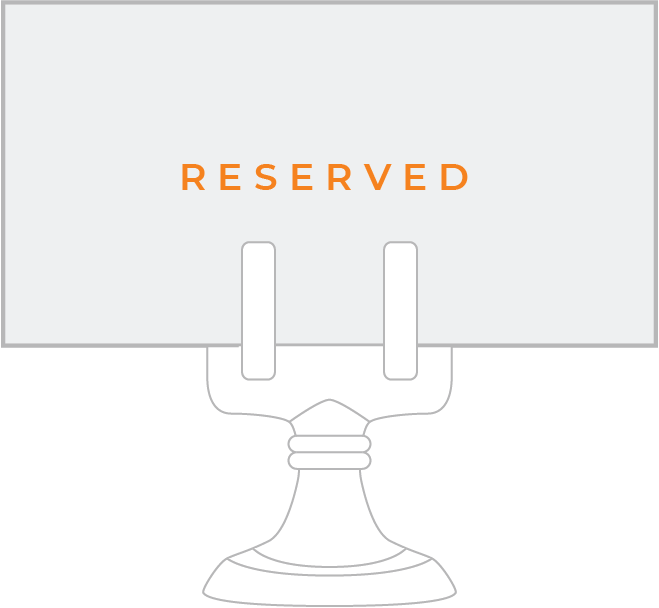
BOH subscribers and BOH Insiders.