Amelia Strat was unboxing a set of benches for her client’s dining room—pieces to anchor the space—when she noticed a funny smell. But it wasn’t until the package was completely opened that she discovered the source: “One of the benches was covered in what looked like dirt, and the other one was literally growing mushrooms out of it,” says Strat, co-founder of New York–based firm Kroesser + Strat Design.
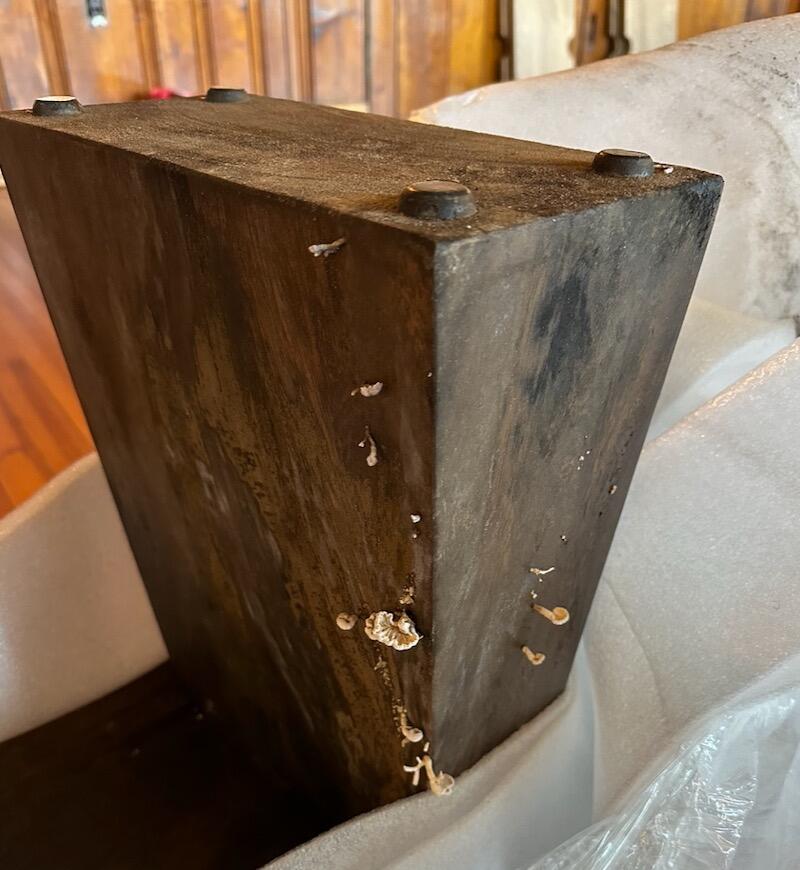
That’s an extreme example of a shipment gone wrong, but it’s not an isolated incident. While some of the challenges of the Covid era—astronomical lead times, in particular—are easing, anecdotal evidence suggests that damaged products and missing shipments are still frustratingly common.
Damages are not a new phenomenon in the design industry. Several years before the pandemic, Houston designer Pamela O’Brien ordered 12 pieces from an e-commerce site and ended up with eight functional chairs and four beat-up ones. Determined to get the chairs, she ordered them three more times, only to receive them broken again and again, until the website was out of stock. But at the time, experiences like that were an aggravating outlier. Today, they are far more commonplace. Last May, Claudia Kalur, a designer based in Litchfield, Connecticut, ordered a bed from West Elm. It finally arrived in October—missing the headboard. “It’s been an absolute nightmare,” says Kalur, echoing a common complaint. “It’s only getting a little better in terms of delivery timing—otherwise, it is not getting better.” Why?
A simple rule of thumb for the design industry: Because projects often take at least a year to complete, whatever is happening for designers right now is the result of last year’s housing market. That can lead to confusing situations, like the fact that we’re in the midst of a real estate slowdown today but designers are still experiencing the aftereffects of the real estate boom, which was still going strong in early 2022.
Those effects, in turn, trickle down to the companies designers rely on to facilitate their business—sometimes in surprising ways. “With super-low interest rates, the amount of people that bought second homes out here [in Denver] during Covid was just astounding,” says Corey O’Neal, the general manager at Denver-based furniture receiver, storer and deliverer Design Logistics Group, which specializes in working with interior designers. Second homes and new builds were particularly common, says O’Neal—projects that are more inclined to be large, have many bedrooms and be furnished entirely with new products passing through his warehouse. In short, it wasn’t just the volume of work that amped up—the volume of new product being specified was also disproportionately increasing. “When [a receiver] gets a lot of jobs like that, you’re just dealing with too much furniture,” he says. “I think people are just stretched too thin, because to inspect a piece of furniture the right way takes a lot of time.”
On June 25, Mason Lane Art Advisory founder Katharine Earnhardt—who works on projects across North America and the United Kingdom—shares her expertise on sourcing and selling art. Click h to learn more and remember, workshops are free for ereBOH Insiders
We want to hear your thoughts! Take BOH’s annual reader survey, an 8-minute questionnaire that helps us get to know you better and will allow us to tailor our storytelling to your business needs.
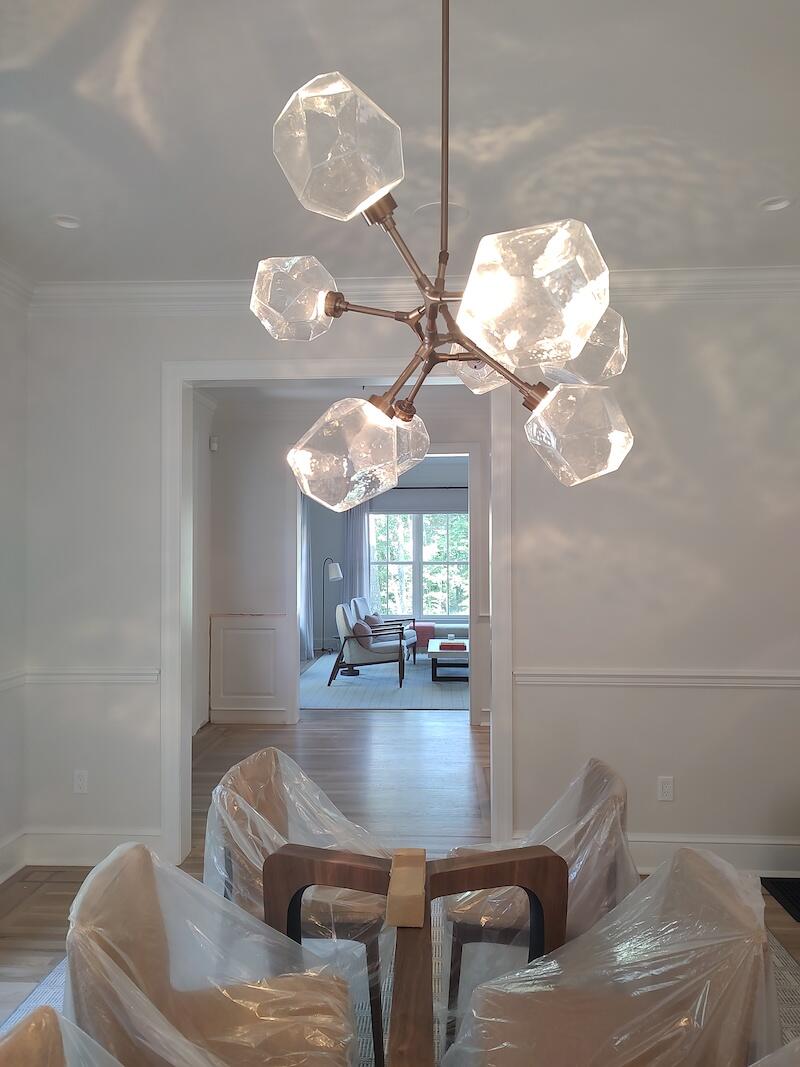
For receivers, time is not the only factor—having enough staff members to carry out those inspections is also key. Sabrina Rivera, director of customer success at New York–based Metropolitan Warehouse & Delivery, tells Business of Home that finding great workers is still an issue, and a lot of warehouses in the industry are utilizing temporary employees. “Because these temps are not everyday employees who have a comprehensive knowledge of standard operating procedures, there are steps that get missed, skipped or not followed through,” says Rivera. She sees those same labor constraints impacting manufacturers, as well, often leading to less durable or secure packaging on incoming products. No matter where the oversight takes place, the end result is the same: damaged products.
Because of the current economy’s low unemployment rate, skilled workers are harder to come by—especially when time is of the essence. “If you’re trying to get something out the door, you’re not really worried about hiring full-time—you’re also not worried about [whether an order is perfectly] correct,” says Rodney Boger, the North Carolina–based founder of private receiving company Boger Installations, who has experienced firsthand the challenges of trying to bring on extra hands in order to meet the demands of the moment.
A glut of incoming furniture and finding reliable employees are two significant hurdles. Rent is another. With more product to manage, receivers need even more space—but warehouse rent is climbing in many areas. Take Denver, for example, where O’Neal says rent is going up throughout the metro area and warehouses are in high demand. Design Logistics is moving to a larger space soon, but O’Neal recognizes how lucky the company is to even find something that’s available. For companies that aren’t able to find more space, accommodating a bustling business in tight quarters is just one more hazard for a piece of furniture as it transits through the warehouse. “It means having to be creative with your storage space because you just do not have enough of it,” he says. “Although it should not affect the quality of the products, having a crowded warehouse makes it easier for things to be damaged just maneuvering them around.”
All designers take a big hit—in time, energy and money—for damaged deliveries, but the effect can vary depending on their pricing model. For those who charge a flat fee like Kalur, there’s the time suck of managing a long string to stakeholders: “frustrating delivery companies, then dealing with the vendors, then explaining the situation to clients and sometimes spending more time finding alternatives if the client does not want to wait”—all extra work, she explains, for no additional pay.
But even for those who are able to bill for that troubleshooting time, designers who charge an hourly rate don’t always feel comfortable passing the full cost of damages on to clients—especially when the product in question came from a trade source they’d vouched for. “There are times when there are egregious issues and errors on the vendor’s part, and our hours are really racking up—we will cut our clients a break and not include [all] that time spent,” says Anna Kroesser, co-founder of Kroesser + Strat Design. “It’s not totally fair to us, but it’s not totally fair to the client either that a vendor is continuing to cost them money.”
The silver lining is that vendors are often sympathetic to the predicament that designers are put in. Kroesser explains that after sending photos of the mushroom-infested bench to the maker, she received a replacement in two weeks. But in some cases, designers aren’t as lucky. After receiving two empty boxes that were supposed to hold her missing headboard, Kalur spent several additional hours on the phone with Williams-Sonoma’s to-the-trade customer service representatives trying to track down the West Elm piece. She finally received an email from the company saying her order shipped, and that it would be delivered in 2030—nine years from when she placed the order.
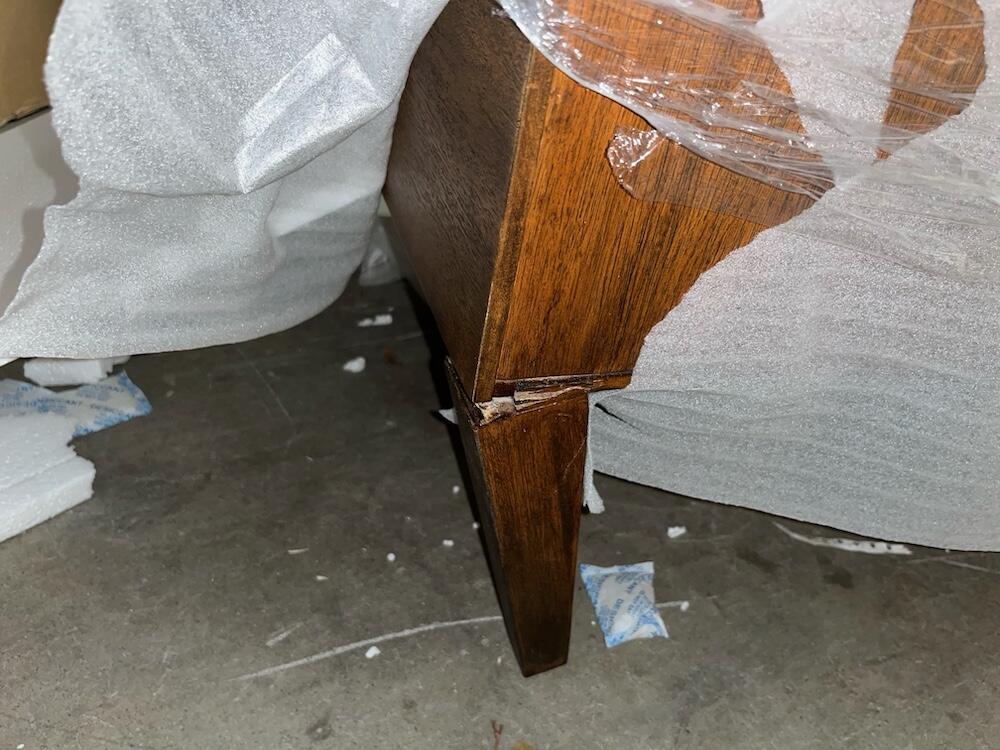
Ultimately, damaged product puts all parties in a bind, and most businesses are doing their best to adapt accordingly. Metropolitan, for example, is bringing in extra hands to ensure quality control. “Now we have more folks watching the product as it’s coming off our trailers, and we’re being more vigilant and making sure that we’re not just doing a front-facing inspection, but a whole walk-around,” says Rivera. Boger is also hiring more employees. “Before, you could get by with one person in the warehouse,” he says. “Now I have to have at least one extra person in the warehouse every day, just to go through all the stuff that comes in. Stuff we would never check years ago, we’re checking now because you never know the issues vendors are having on their end.”
Despite the challenges and complexities of dealing with damaged deliveries, one thing is clear to both designers and receivers: You get what you pay for. Multiple designers reported that products from luxury vendors were damaged less often than those from big-box stores. The same seems to be true on the warehouse end. Several receivers told BOH that it was more common for them to deal with damages from big e-commerce companies, and that vendors—seemingly used to the churn of damaged goods—often suggested disposing of the products and sending a replacement rather than expending the effort to return the broken items.
But for both the high and low end, there’s bittersweet news ahead. The housing market has already cooled off—a lot—since the froth of the pandemic, suggesting that both factories and warehouses will get back to business as usual fairly soon. While that may mean that profits cool off, too, the return to a more manageable flow of business will be a welcome relief for many. For her part, Rivera is hopeful the increased level of shipping challenges will begin to resolve in the very near future: “I’m finding more and more that Covid is a thing of the past,” she says. “I really do foresee that by the end of this year, we will see a great improvement.”
Homepage image: ©Showcake/Adobe Stock